It seems easy enough: build new houses so people can move into them and enjoy life as a homeowner. Problem is, cities are hesitant to allow unlimited new construction, the workforce just isn’t there and materials are expensive.
Follow Tech Reporter Rich DeMuro on Instagram for more tech news, tips and gadgets!
“This is not something that we can overcome overnight. This is simply supply and demand,” explained Gary Painter, a professor at the University of Southern California who specializes in urban planning and housing economics.
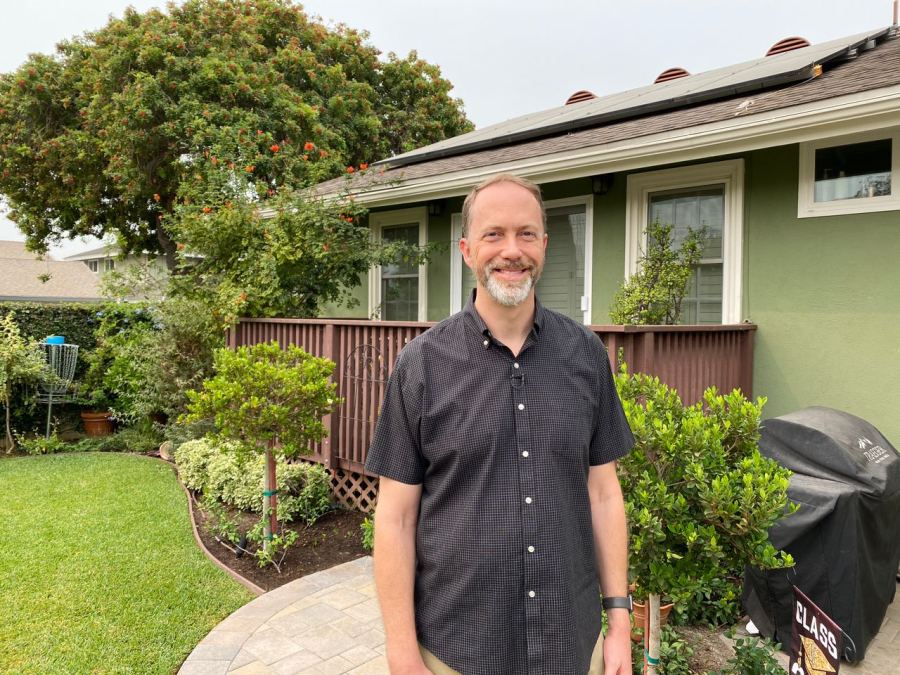
Now, a Silicon Valley startup thinks they have an answer: 3D printing.
“With our printers, we’re able to print the entire shell of the structure or panels depending on what product we’re talking about,” said Sam Ruben, co-founder of Mighty Buildings.
I checked out their demo unit at a parking lot near LAX.
They’ve come up with a special gel that cures instantly into a solid material when zapped with light. Using it, they’ve successfully 3D printed a 350 square foot studio apartment at their San Jose factory in just 24 hours.

But for now, they’re starting small. Like, just one wall.
“The curved wall here is the part that’s 3D printed,” pointed out Ruben. The hybrid building I saw is a combination of 3D printed and traditional materials. It starts at $115,000, which doesn’t include the final “on-site” finishing work.
But if you’ve ever priced out an ADU, what Mighty is building could be pretty appealing. The structure fits in a majority of California backyards and can take advantage of streamlined approval processes for structures like this.
“So an ADU is an accessory dwelling unit. It’s a technical term for what’s often called granny flats or backyard apartments,” explained Ruben.

Inside the studio has everything you need: a bedroom/living room, kitchen, and bathroom.
Mighty Buildings even leaves a bit of the 3D printed wall exposed as a reminder of the tech holding up this house. The material, which feels like a rock, is about as strong and durable as concrete but more energy-efficient and easier to manage.

About 80% of the studio is created in a factory, then trucked to the site.
“With what we’re doing, we’re introducing 3D printing to do some of the most dangerous parts of the job,” says Ruben. He believes that 3D printing homes could be part of a blueprint to solve the housing crisis so many cities are experiencing.
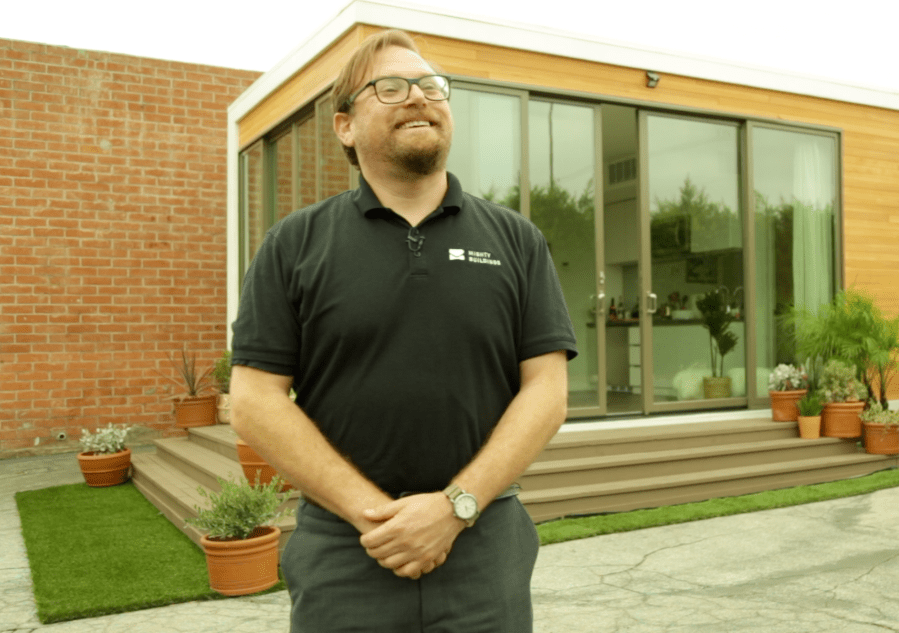
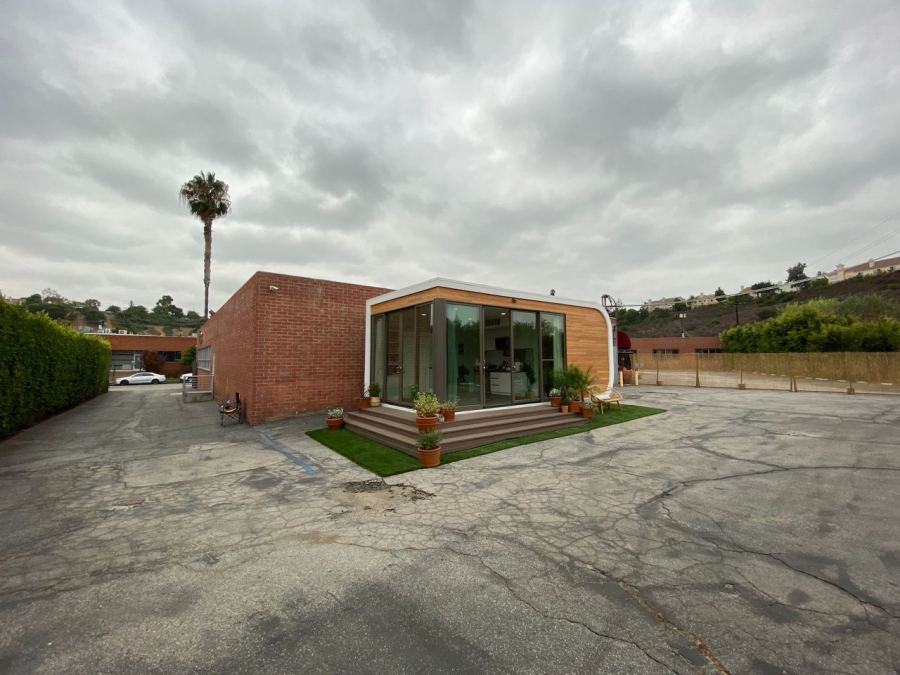
“We have to change and I do think that there is political will now to kind of review how we’ve done things in the past,” said Professor Painter.
“It’s imperative that we embrace whole new ways of building, [to] truly unlock that productivity and that efficiency,” concluded Ruben.
Mighty Buildings is making units the way up to 3 bedrooms for under $300,000. Delivery starts early 2021.
NOW: Listen to the Rich on Tech podcast, where I talk about the tech news I think you should know about and answer the questions you send me!